Shareholders
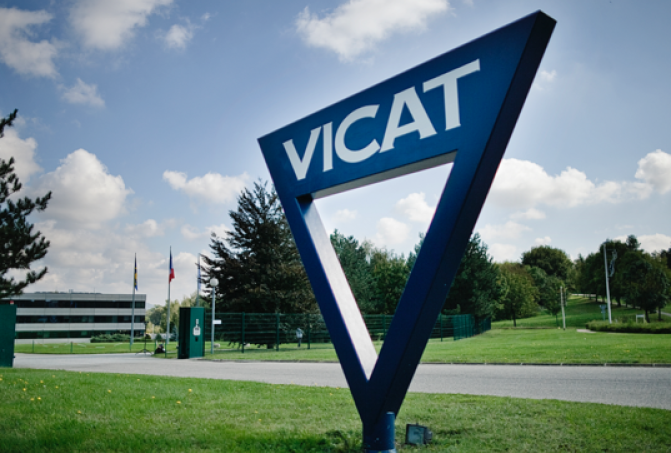
Vicat Shareholders and Investors Service:
Tél : +33 1 58 86 86 86
Email : relations.investisseurs@vicat.fr
Shareholder information
Web site : www.vicat.fr
Symbol : VCT
ISIN Code: FR0000031775
Euroclear France : 816
Bloomberg : VCT.PA
Reuters : VCTP.PA
To become a shareholder of the Vicat Group, please consult your financial adviser or broker.
Capital structure
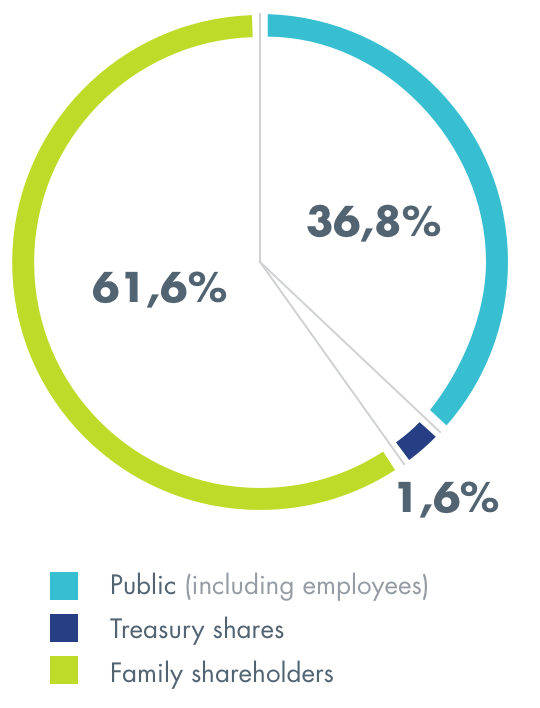
Share capital
As of December 31, 2021, the company’s share capital amounted to 179,600,000 euros, consisting of 44,900,000 shares with par value of four euros each.
The Company's shares are traded on the Eurolist market of Paris' Euronext Stock Exchange, Compartment A.
Its shares have also been eligible for the Deferred Settlement Service since February 2008.
Dividend
Based on results in 2021, and confident in the Group’s ability to sustain its ongoing development, the Board of Directors has decided to propose that the Annual General Meeting of shareholders on April 13, 2022. Dividend increase of 1.65 euros per share.
Share details
Place listed
Euronext Paris
Exchange segment
Compartiment A
Share code
FR00000 31775 –VCT
Sector classification
Matériaux et accessoires de construction
Registered shares
Tour Manhattan 6 place de l’Iris 92095 La Défense Cedex
Tickers
Reuters VCT PA et Bloomberg VCT FP