Innovation has been in the Group’s DNA for 200 years. It is the spearhead of our engagement to build and live together, and to protect the planet. We focus on fields of innovation for building the cities and infrastructures of tomorrow, we set up scientific partnerships, and we work with the key players in each sector.
Using hydrogen in a cement plant can reduce our carbon footprint at the level of two separate links in our value chain: firing of clinker and transport of finished products.
A first reduction can be brought about by using CO2 emitted by cement kilns beneficially, in conjunction with hydrogen, to produce compounds that are used in the chemical and petrochemical industries. The second reduction involves using hydrogen directly to run our trucks transporting the cement we produce.
The Group is studying the potential for establishing two distinct electrolysis systems at the Saint Égrève cement plant, near Grenoble. The first of these, a mature technology, will produce enough hydrogen to run 10 trucks for which Group subsidiary SATM Transport has placed a pre-order.
The second system, which is based on a technology still under development, makes use of the residual (waste) heat of the cement manufacturing process to increase the efficiency of electrolysis by more than 30%. The two complementary projects will be carried out collaboratively, the first with Hynamics, a subsidiary of French power company EDF, the second with the Innovation Laboratory for Nanomaterial and New Energy Technologies (LITEN) of France’s Alternative and Atomic Energies Commission (CEA).
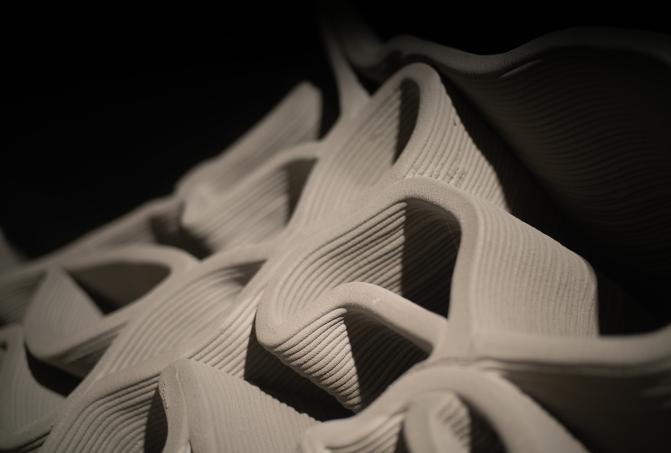
Nature is the only engineer capable of creating multitudes of production cycles without consuming fossil fuels or generating waste.
Biomimetics is based on this, following the examples of efficient systems encountered in the world of animals and plants to come up with sustainable breakthrough innovations.
Just off Cap d’Agde, on France’s Mediterranean coast, an artificial reef of a new generation has been placed on the seafloor. The 32 modules were 3D-printed using a concrete ink produced by Vicat.
The special mix design is tailored to be highly plastic, strong, and durable, and thus meet the physical and biodiversity imperatives of the subsea environment.
The Cimentalgue trial being run at the Montalieu cement plant in east-central France is testing the potential for using captured CO2 to increase microalgae harvests.
In addition to capturing CO2 from the exhaust fumes, the project subsidized by France’s Environment and Energy Management Agency (ADEME) involves recovering waste heat from the kiln stack. The CO2 is fed to microalgae crops whose environment is heated year-round in a closed-loop system requiring no external energy. This is known as industrial symbiosis, in which the provision of CO2 and industrial waste heat reduces the production cost of microalgae which can be used as a food supplement or biofuel.
About 50% of all the raw materials used in the European Union are employed in the construction sector, which at the same time generates about a third of all the deconstruction and demolition materials, i.e. concrete, bricks, tiles, and other ceramics that can potentially be recycled into aggregate.
Until now only a meager 4% of these repurposed materials has been used to make concrete. This low figure has incited Vicat and sixteen partners from five countries in Europe to launch the SeRaMCo project (Secondary Raw Materials for Concrete precast products) with the support of the European inter-regional cooperation program, Interreg.
Reducing the carbon footprint of concrete while at the same time improving the quality of recycled concrete aggregate. Together with around twenty partners, Vicat is working on the FastCarb (Accelerated Carbonation of Recycled Concrete Aggregate) project.
The idea behind which is based on the observation that throughout its lifetime concrete undergoes a natural process of carbonation of the cement it contains; very slowly, it absorbs at least 15% of the carbon equivalent emitted by kilns during the manufacture of the cement.
Bearing this phenomenon in mind, at its Créchy cement plant in central France, Vicat is conducting trials with a cross-flow rotary dryer that in around one hour can reproduce the natural physico-chemical phenomenon observed.