Cement
Modern cement, the mysteries of which were unveiled by Louis Vicat in 1817, is our historical core business.
Today, our production capacity amounts to over 28 million metric tons. As its most important ingredient, cement gives concrete a number of properties, especially its strength. It is a fine mineral powder obtained by firing and milling a mixture of crushed limestone and clay.
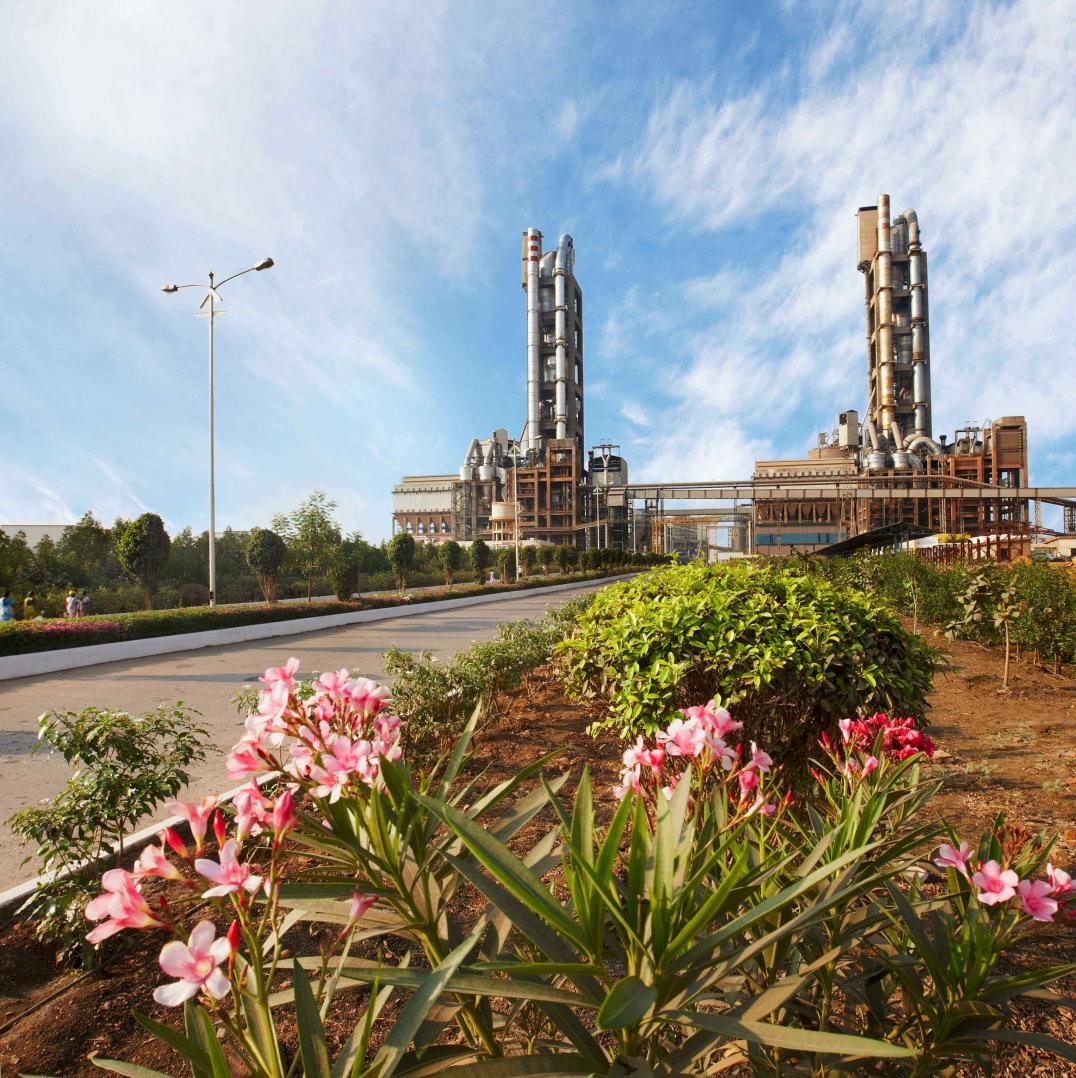
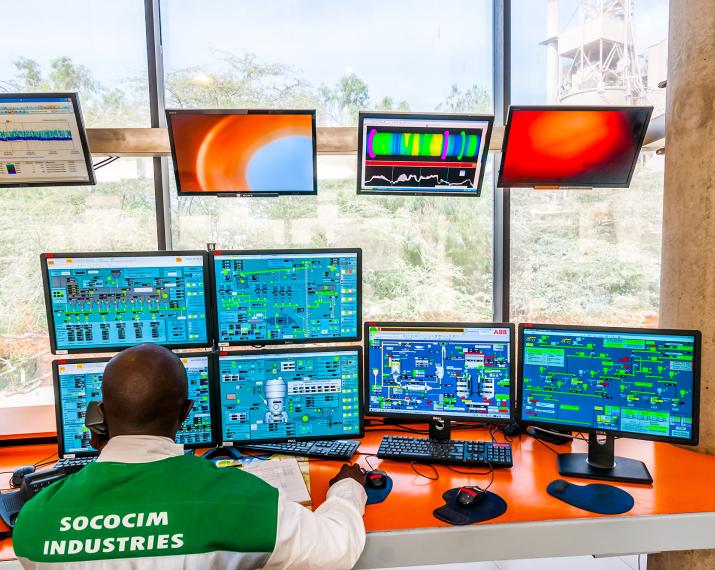
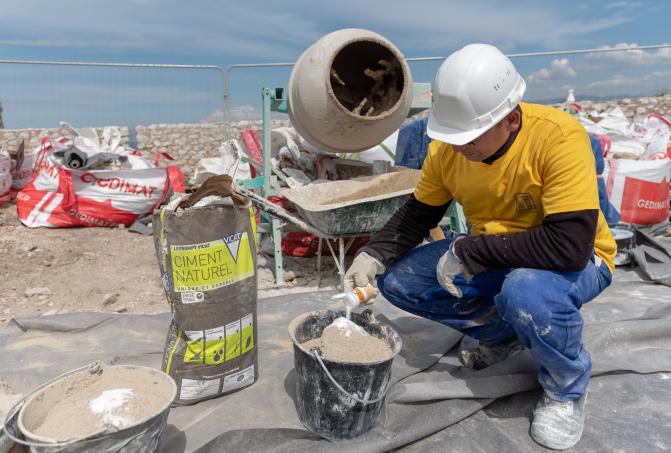
Focus on
titre
Prompt quick-setting cement
Not only is Prompt natural quick-setting cement practical for works requiring serviceability in the shortest possible time, due to the very high speed at which it sets and hardens, but it also has a low environmental footprint. It is unusual in that:
- it is mined rather than extracted from open-air quarries
- it is fired at a low temperature, which means low CO2 emissions.
Its properties take the knowhow of craftsmen to higher spheres and enable heritage architects to have 19th and 20th-century works of historical interest restored using the original methods.
The different kinds of cement available
Vicat's cement expertise
The Vicat group produces a broad range of solutions:
- several kinds of modern cements
- natural cement
- hydraulic road binders
The different types of cements are for different applications such as housing, bridges, tunnels, and situations where the concrete is subject to aggressive environments.
The different properties of these cements depend on:
- the chemical composition of the raw materials
- where applicable, the addition of complementary ingredients during milling (limestone filler, pozzolan, fly ash, blastfurnace slag, and gypsum)
- the fineness to which they are milled.
The main types of cements produced by the Vicat group correspond to and comply with European standards:
CEM I (Portland cement) and CEM II (Portland composite cement): these are the cements most commonly used in conventional reinforced-concrete structures—bridges, industrial and commercial buildings, and housing. Some special formulations of these cements are also used in underground works in aggressive environments or under the sea.
CEM III (blastfurnace cement) and CEM V (composite cement): cements giving off low heat during hydration and with low sulfate contents, used for underground works in aggressive environments or for maritime works
CEM IV (pozzolanic cements): cements using mineral ingredients of volcanic origin that display hydraulic properties. We manufacture and market this kind of cement only in Italy
Natural Cement Prompt : a special quick-setting, rapid-hardening cement used for fast masonry work, underwater work, and drains and sewers, and also for restoration and decoration of heritage assets and in eco-construction. It is the Group’s historic cement, having been produced since 1970 from a natural Alpine rock. Its performance is exceptional, developing high strength immediately and with little shrinkage.
Hydraulic road binders were developed to reduce the demand for quarrying of prime materials and to encourage the use of site materials for roadworks.
Did you know? >All our standard cements are certified against the specifications of standard EN 197 1 by AFNOR Certification. Our special cements are certified in accordance with complementary characteristics defined in the requirements for the NF LH mark and associated standards.
Locations
Our facilities
- Brazil
- France
- Switzerland
- Italy
- United States
- Egypt
- Senegal
- Mauritania
- Mali
- Turkey
- Kazakhstan
- India
Cement is manufactured in 6 steps:
The main steps in cement manufacture
Step 1: extraction of raw materials
The raw materials required—limestone and clay—are extracted from quarries close to cement plants:
- massive rock and boulders are broken out by explosive blasting
- the resulting material is transported by quarry haulers to crushers where it is reduced to no more than the size of small cobbles (less than 10 cm in diameter)
- the crushed raw material is sorted: it must contain the right quantities of lime, silica, alumina, and iron oxide.
Step 2: preparation of the raw meal
After crushing, the raw materials go through several steps of processing:
- preliminary mixing in pre-blending halls to obtain more regular combinations
- drying and crushing:
- crushers reduce the size of the material to a few dozen micrometers
- kiln gas circulated through the crusher dries the material and some of the sulfur in the gas is transferred to it.
The crushed material thus obtained is known as ‘raw meal’. A great many chemical analyses are performed on it during its processing to check that the proportions of the various substances it contains correspond to the chemical composition required.
Step 3: firing
Firing of the raw meal is highly complex and takes place in several stages:
- precalcination stage: the raw meal in powder form is fed into the top of a preheater tower. As it falls to the bottom it is heated to increasingly high temperatures by exhaust gas from the rotary kiln, reaching as much as 850°C (dry-process kilns) at the bottom
- clinker production: the raw meal is then fed into the top end of an inclined rotary kiln lined with refractory bricks. The flame inside the kiln reaches temperatures in excess of 2,000°C. This firing process brings about several complex chemical reactions:
- the limestone decarbonates at high temperature (900°C) and is transformed into lime
- the clay breaks down into silicates and aluminates
- the resulting material then recombines at a temperature of about 1450°C to produce nodules of calcium silicates and aluminates known as ‘clinker’, a semi-finished product with hydraulic binding properties
- clinker cooling: the clinker gives up its heat as it passes through a cooler fed with air at 100°C.
Throughout this complex process, the chemical composition and uniformity of the material fed into the kiln, together with the regularity of the feed rate, are fundamental parameters.
Did you know? Our kilns are equipped with electrofilters or bag filters to reduce dust discharge to the atmosphere.
Step 4: cement milling
The clinker is then processed in several ways:
- it is milled to a particularly fine grain size (less than 60 micrometers)
- the resulting powder—cement—is blended with gypsum to regulate its setting time
- other processing may follow:
- to improve the workability and consistency of the cement, limestone filler or fly ash (a by-product of coal-fired power plants) may be added
- to improve the hydraulic properties of the cement, natural or artificial pozzolans may be added.
Step 5: storage of cement
The cement produced is stored in silos of several thousand tons. Some silos are divided into several compartments for storage of different types of cement.
Step 6: cement delivery
Cement is delivered in bulk or in bags:
- Bulk delivery: cement trucks on a weighbridge are filled by means of telescopic loading heads at the bottoms of silos. Loading is checked and the data required for shipping and invoicing documents are transferred to the central computer.
- Bags: cement is bagged on rotary machines with throughput of as much as five thousand 35-kg bags per hour. Valve bags are self-sealing. Palletizers stack 1.5 tons of bags on each pallet. A supervisory control system in the control room manages all these operations around the clock.
News
Achievements